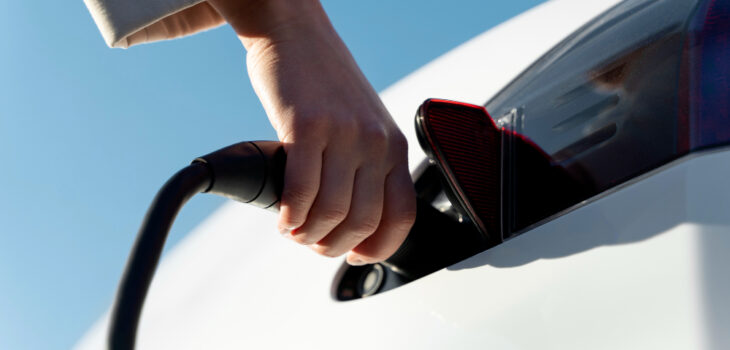
Fuel Nozzle Technology Boost Combustion in Engines and Burners
Fuel nozzles may appear small and simple, but they play a critical role in engines and combustion systems across a wide range of industries. Whether in vehicles, aircraft, power plants, or industrial burners, the fuel nozzle ensures that fuel is delivered at the right pressure, angle, and spray pattern to support optimal combustion.
In this blog, we’ll explore what fuel nozzle are, how they work, their types, applications, and common signs of failure.
What Is a Fuel Nozzle?
A fuel nozzle is a precision-engineered component designed to atomize and deliver fuel into a combustion chamber. It regulates the flow of fuel, ensuring the correct spray pattern and droplet size for efficient burning. This helps optimize fuel consumption and reduce emissions.
How Does a Fuel Nozzle Work?
Fuel nozzles work by forcing pressurized fuel through a small orifice, which breaks the liquid into fine droplets—a process known as atomization. The nozzle controls:
-
Flow rate: How much fuel is delivered.
-
Spray pattern: The shape and spread of the fuel mist.
-
Droplet size: Smaller droplets burn more efficiently.
-
Angle of spray: Directs fuel into the combustion zone for maximum efficiency.
In engines, this atomized fuel mixes with air and ignites to produce power. In turbines or burners, it helps maintain a stable and complete flame.
Types of Fuel Nozzles
-
Pressure Atomizing Nozzles
-
Common in diesel engines and industrial burners.
-
Use high fuel pressure to atomize fuel.
-
-
Air Blast Nozzles
-
Use compressed air and fuel to produce a fine mist.
-
Often used in gas turbines and aircraft engines.
-
-
Dual-Orifice Nozzles
-
Feature two spray patterns for different operating conditions.
-
Improve combustion under varied loads.
-
-
Swirl Nozzles
-
Spin fuel to enhance atomization and spray control.
-
Used in high-precision applications.
-
Applications of Fuel Nozzles
Fuel nozzles are used in a variety of sectors:
-
Automotive – In fuel injection systems of gasoline and diesel engines.
-
Aerospace – In jet engines for precise fuel delivery at high speeds.
-
Marine – In large diesel engines of ships and vessels.
-
Power Generation – In gas turbines and combustion systems.
-
Industrial Burners – For heating, drying, and other thermal processes.
Common Issues and Signs of Fuel Nozzle Failure
Like any component, fuel nozzles can wear out or become clogged over time. Common signs include:
-
Rough Engine Start or Idle
-
Poor Fuel Economy
-
Black Smoke or Soot Emissions
-
Incomplete Combustion
-
Backfiring or Misfiring
Regular cleaning, inspection, and replacement are essential to maintain peak performance.
Maintenance Tips
-
Use clean fuel and proper filtration to reduce contaminants.
-
Inspect spray patterns regularly in industrial systems.
-
Replace nozzles at manufacturer-recommended intervals.
-
Keep spare nozzles for quick replacement to avoid downtime.
Advanced Materials Used in Fuel Nozzles
Fuel nozzles are exposed to extreme temperatures and pressures, so they are often made from high-grade materials such as:
-
Stainless steel – for corrosion resistance and durability.
-
Nickel-based alloys – for high-temperature tolerance, especially in aerospace and turbine applications.
-
Ceramics and composites – used in advanced systems to reduce wear and enhance longevity.
Design Considerations
When designing or selecting a fuel nozzle, engineers consider:
-
Viscosity and type of fuel (e.g., diesel, kerosene, jet fuel)
-
Required flow rate
-
Spray pattern angle and distribution
-
Combustion chamber design
-
Environmental conditions (e.g., marine, arid, high-altitude)
Impact on Emissions
Fuel nozzles contribute to cleaner combustion by:
-
Improving air-fuel mixing
-
Promoting complete fuel burn
-
Reducing the formation of unburned hydrocarbons, carbon monoxide, and soot
In regulated industries, precision nozzles are key to meeting emission standards like EURO 6 or IMO Tier III.
Digital Monitoring and Control
Modern systems now integrate electronic fuel injection (EFI) or smart nozzles that:
-
Monitor pressure and flow in real time
-
Adjust spray patterns dynamically based on load and speed
-
Enhance fuel economy and reduce manual intervention
Common Maintenance Practices
-
Ultrasonic cleaning: Removes fine deposits without damaging the nozzle.
-
Flow testing: Verifies if the nozzle delivers the correct rate.
-
Visual inspection: Detects cracking, wear, or clogging.
-
Calibration: Ensures proper spray angles and atomization are maintained.
Conclusion
Fuel nozzles are small but powerful components that have a major impact on engine efficiency, emissions, and performance. Choosing the right nozzle for your application—and keeping it in good condition—can save fuel, reduce maintenance costs, and improve overall system reliability.
Whether you’re working with vehicles, turbines, or industrial burners, understanding the role of the fuel nozzle is key to optimizing combustion and performance.